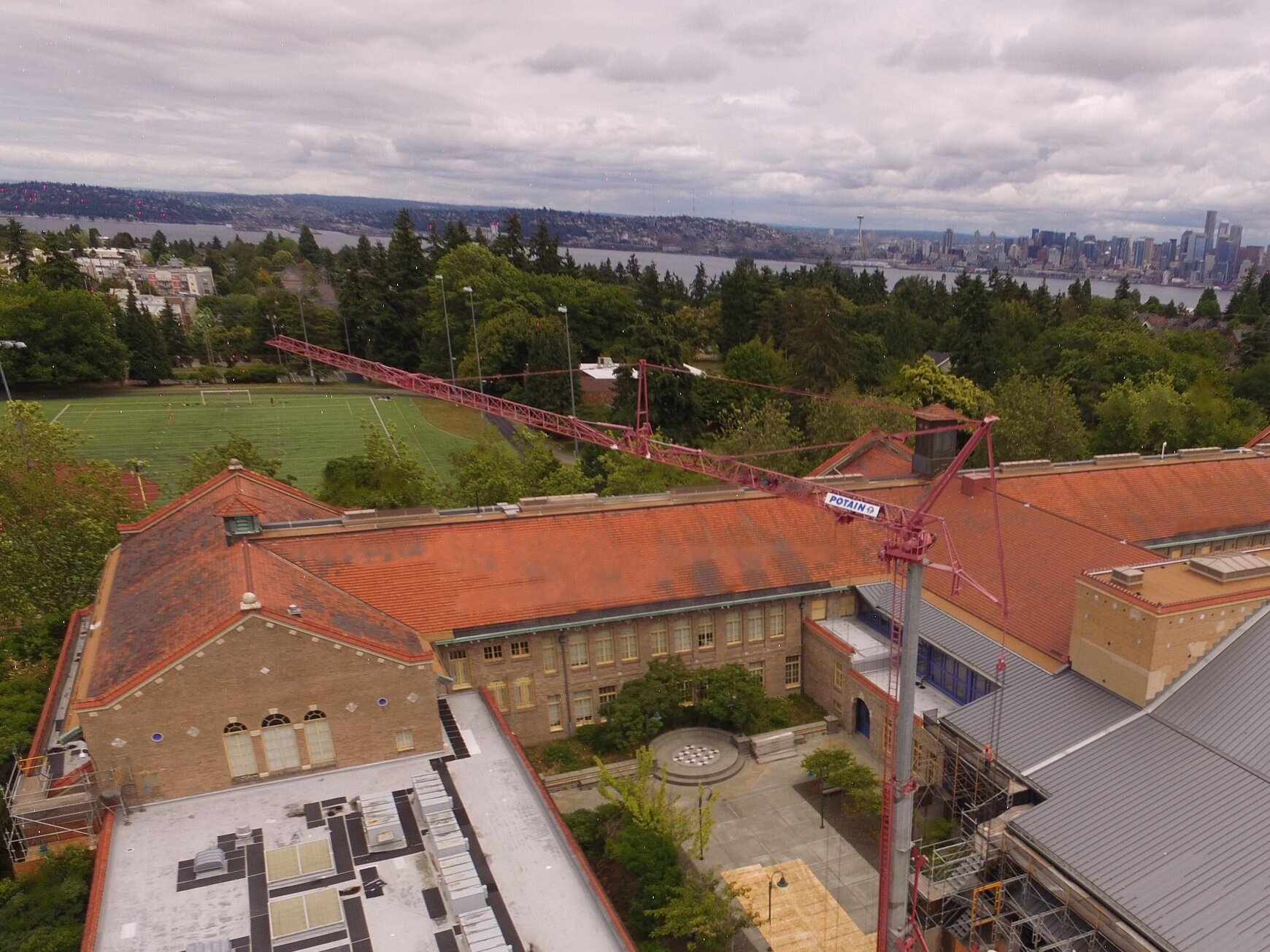
West Seattle High School
Wayne’s Roofing, as the primary contractor, and Architectural Sheet Metal (the sheet metal sub-contractor) displayed a high level of professionalism and cooperation with SMSA and BET&R throughout the duration of the project.
West Seattle High School
Project: West Seattle High School Roof Replacement
Location: Seattle, WA 98116
General Contractor: Wayne’s Roofing, Inc.
Architect: Stemper Architecture Collaborative (Architect), Building Envelope Technology & Research (Building Envelope Consultant)
Owner of the Building: Seattle Public Schools
Year Completed: 2020
Expected Start Date: July 2017
Estimated End Date: December 2020
Public/Private/Federal: Public
Square Feet: 123,000
Consisting of the following:
Steep Slope Tile Roofing 44,100 sf
Low Slope APP Membrane Roofing 60,400 sf
Standing Seam Metal Roofing 18,500 sf
System Type:
Steep Slope: 100+ year old Historic Ludowici Clay Tile
Steep Slope: AEP Span Standing Seam Metal Roofing
Low Slope: Derbigum APP (atactic polypropylene) Multi-ply Granulated Roof System
Protected Siplast PMMA (polymethyl-methacrylate) Fluid Applied Roof System with rubber paver walking surface
Protected APP Membrane Roof System with rubber paver walking surface
Siplast PMMA Built-in Gutters
Key Sub-Contractor:
Architectural Sheet Metal:
Nick Pederson, PM
David Stroud, Site Foreman
Alpine Masonry:
Dan Durbin, PM
Dan McHaffie, Site Foreman
Johansen Mechanical:
Ivy LeVangie, PM
PM/PX and Superintendent:
Mike Trout, PX
John Vanderhoof, PM
David Wetherbee, Superintendent
Project Description:
There were several factors that led to Wayne’s Roofing Inc. (WRI), being selected as the roofing contractor for this project. Some of these factors included the overall complexity, the historic value, and schedule restrictions of the project. Both the architect, and building envelope consultant recommended to Seattle Public Schools (SPS) that they reach out to WRI to perform this roofing project. Fortunately for WRI, SPS elected to utilize the E&I cooperative purchasing program to contract this project. This was a multi-phased project spanning over the course of three years, which required multiple subcontractors, roofing foremen, superintendents, and project managers.
Chuck Richmond was selected as the Superintendent for the Phase 1 portion of this project and Dave Wetherbee as Superintendent for Phase 2 of this project. Combined, Chuck and Dave have over 60 years working at WRI and between the two of them have extensive knowledge of every aspect of commercial roofing. Tim Carnicle was primary foreman of the low slope APP roofing on this project. Tim is a long time WRI employee of more than 25 years. Tim is very detail oriented and has a vast amount of knowledge about low sloped heat fused roofing installation in addition to other low slope roofing systems. This includes PMMA Fluid Applied systems.
Dan Powers was selected as our steep slope tile roofing foreman for this project. Dan has been a WRI employee for over 14 years and is a well-rounded roofing technician that is knowledgeable in most steep slope roofing systems was the perfect choice as foreman for this historic steep slope tile roofing remediation project. Mike Trout started Phase 1 as the Project Manager under Brian Butler as the Project Executive. John Vanderhoof started Phase 2 as the Project Manager under Mike Trout as the Project Executive for the final phase of this extensive roofing and masonry remediation project. Brian Butler is a Principal at WRI with over 20 years employment with the company. Mike Trout is a Project Executive with over 20 years employment at WRI. John Vanderhoof has over 15 years of experience in the roofing industry and joined the WRI team a little over a year ago.
Phase 1 was a combination of tile roofing remediation and APP multi-ply granular roofing system. The APP roofing system was installed at the “catwalk” along the ridge of the steep slope tile roofing in addition to the built-in gutters along the eaves of the steep slope tile roof areas. Phase 2 consisted of Steep Slope Tile Roofing, Steep Slope Standing Seam Metal Roofing, Low Slope APP Multi-ply Granular surfaced roofing, and some historic brick masonry restoration work.
This project involved multiple trades and scopes of work all working simultaneously and sequentially.
The roofing portion of this project consisted of the following:
Retrofit of the 100-year-old historic tile roofing system, which included removal of the existing 100-year-old historic roof tiles and setting them aside to be reinstalled later
Removal of the existing felt underlayment down to existing tongue and groove wood substrate
Installation of a new plywood diaphragm over the existing tongue and groove wood decking
Installation of a two ply underlayment system over the new plywood diaphragm
Installation of a wood batten and counter batten system to elevate the tile to reduce heat on the new underlayment system
Brush cleaning of historic clay tile
Reinstallation of the tile along with associated new copper sheet metal flashings
The low slope roofing replacement consisted of the following:
Removal of the existing single-ply membrane roofing and underlying insulations down to underlying substrate (substrates varied from steel decking, concrete deck and composite asphaltic sloping fill over concrete deck)
Installation of new heat fused vapor barrier (over mechanically attached gypsum substrate board where needed)
Adhered insulation and cover board
Installation of a multi-ply heat fused Derbigum APP granular surfaced membrane roof system
New architectural sheet metal flashings along with reinstallation of custom radiused aluminum coping metal that was salvaged at the roofing demo stage of the project to be reinstalled in order to keep the historic aesthetics
The Steep Slope Tile Roofing system consisted of the following:
Removal of existing steep slope standing seam metal roof system
Salvaged underlying rigid insulation to be reinstalled under new metal roofing to reduce materials headed for the land fill
Removal of existing substrate board to expose underlying metal decking
Installation of new gypsum substrate board with adhered vapor barrier
Reinstallation of salvaged rigid above deck insulation
Installation of new AEP Span standing seam metal roofing along with new architectural sheet metal flashings
Due to the footprint of this site and limited access to all roofing locations, WRI elected to erect a tower crane for Phase 2 to assist with access to most roof areas for materials and equipment handling. This approach has proven extremely valuable based on the logistics of the site.
In addition to the roofing scope of work, this project also entailed some historic brick masonry restoration performed by Alpine Waterproofing and Masonry Restoration. The brick masonry restoration scope consisted of the following:
Routing aged mortar joints, re-tuck pointing these joints with new mortar and cutting new ragle joints for installation of roofing counter flashing metals at various locations. This process was needed to minimize the chance of water migrating through the historic brick mortar and finding its way behind the newly installed roofing systems.
This team has proven to be efficient, goal oriented and dedicated to providing the best product possible to our collective client.
If you can’t find what you are looking for, please contact our Sales Department: